3 tips to help you successfully fit out your vehicle
- 05/09/23
- 5 min
After making the all-important choice of a utility vehicle (make, energy, loading capacity, cost, etc.) comes the next key stage: fitting it out. At this stage, careful thought must be given to the actual use which will be made of the vehicle, especially for activities such as construction and the environment, for which safety and user-friendliness are absolutely critical. Here are the main golden rules to be followed when looking to optimise your working vehicle.
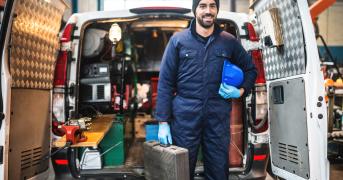
Tip no.1: Carefully identify your requirements, even if it means seeking advice on this
This might seem like the obvious starting point for any fit-out, but it really is important to carefully define the needs of your business. And to take the time to carefully examine in detail exactly what you expect from your vehicle. Careful consideration must be given to the special characteristics of certain occupations and activities, and this is especially the case in the construction and public works sector, in which heavy and often fragile loads are carried on a daily basis and in which load management is an important factor to be managed (front-rear weight distribution, chocking and cushioning of equipment, positioning of handling equipment, etc.). In the case of environmental activities, in addition to loads and tools, there’s also the problem of collection and interior layout to be considered. As these requirements are different, the layout of the utility vehicle will not always be the same.
And as each activity is unique, the layout of each vehicle should be differentiated and suitably adapted. The possibility of obtaining advice during this important stage should not be overlooked. The know-how of certain professionals (vehicle hire firms, companies involved in fitting out vehicles, etc.) can be extremely useful as they have extensive experience of these activity-specific issues. It would be a shame to miss out on such advice when tackling issues as important as modularity or the anticipation of due dates. A professional will automatically have an idea of the right solution to use, as is the case when choosing materials or equipment. For example, a fit-out produced mainly from wood will have an impact on the weight of the vehicle and consequently on its fuel consumption and therefore its TCO (total cost of ownership).
Tip no.2: Ensure that safety and user-friendliness are central aspects of the fit-out.
In Europe, “it should be noted that the construction sector is the most accident-prone: it is in the construction and public works industry that we find the highest number of serious accidents and in which the frequency and criticality rates are the highest” announced the latest occupational health and safety report from Eurostat, the European Union’s statistics office. In France, the data from the occupational risks department (sickness insurance scheme) from December 2019 mentioned 1.577672 million employees working in the construction and public works sector, accounting for 88,531 “first payment” accidents, including 80,802 occupational accidents resulting in sick leave of 4 days or more. At the same time, the number of accidents while travelling is rising (+5.2%) for the first time in a decade while musculoskeletal disorders have increased by 2.7%.
With this in mind, carefully organising load distribution is vital, with the loads concerned often being considerable, and this can involve structural work (reinforced floors, possibly partitions, etc.). Several professional organisations in the construction and public works sector therefore recommend using an approved overload warning system, to be fitted by a certified installer (for further details, please see the recommendations from the OPPBTP www.preventionbtp.fr, and from the INRS www.inrs.fr). Similarly, load retention and securing solutions are vital: load anchorage points, straps, protective nets, etc. In the event of a collision, the mass of the items projected forward is multiplied twenty-fold, as reported by the INRS (Institut national de recherche et de sécurité National research and safety institute). A simple hand tool can weigh as much as a case of bottled water! It should also be remembered that all conversion and fitting-out work must be performed in compliance with the applicable legal texts. At the same time, particular care should be paid to ergonomics and user-friendliness including: the ease of entering and leaving the vehicle, efforts to combat poor posture, and optimised storage to reduce the number of actions required to access tools and equipment, etc. We cannot stress highly enough that comfort plays a key role in enhancing professional efficiency. In Europe, approximately 20% of work stoppages are related to lower-back pain.
Tip no.3: Maximise productivity.
The previous tips all contribute to the same goal: that of maximising productivity. A vehicle which is correctly fitted out and which is tidy will save you precious time. It has been estimated that an operator can lose up to 30 minutes a day looking for his tools in an untidy works vehicle! With this in mind, the choice of accessories should not be left to chance and, according to the case in question, the “occupational” 3D simulations available in the marketplace can prove very useful. This entails encouraging people to adopt best practices concerning well-being on board the vehicle (packing away clothing and personal belongings, items for a break, etc.). From a business perspective the use of IT equipment (tablets, laptops) can help greatly with administrative procedures (stock management, tracking schedules, producing ‘to-do’ lists for vehicle preparation) and allow personnel to maximise their time efficiently.
- Begin by identifying your true needs.
- Prioritise safety and the practical aspects (equipment, signalling and signposting, ergonomic aspects, etc.).
- The fitting-out stage should be considered as part of the company’s wider efforts to maximise productivity.
- Keep in mind that the vehicle is also a “connected office” (administrative tasks, avoiding unnecessary journeys, etc.).
Also worth reading
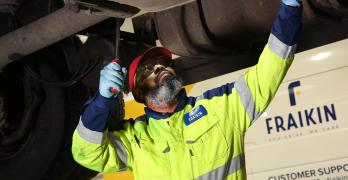
The DVSA’s New LCV Enforcement Strategy: What You Need To Know
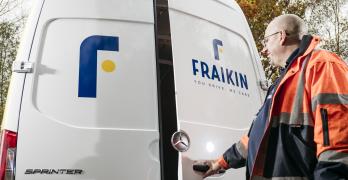
DVSA Embraces Digital Communication for Prohibition Notices
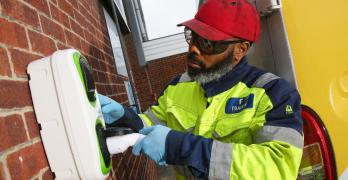