Industrial vehicles: why and how should you train your employees in eco-driving ?
- 29/03/23
- 3 min
Eco-driving refers to driving in a way that is economical, environmentally friendly and safe. The idea has gained popularity in the past ten years, and is now a real concern for businesses. For those companies that use industrial vehicles, this comes with a need to train drivers. Focus.
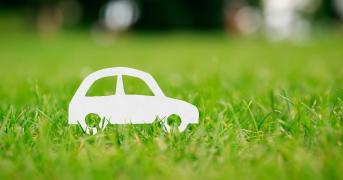
While eco-driving has existed for several years, companies’ interest in it has yet to wane. Made popular in 2009 in response to increasing fuel prices, it has gained ground due to increasing social and environmental policy considerations. And for good reason: this technique improves employee safety, saves money in fleet management and consolidates its environmental performance. When you see the striking figures (we estimate that it reduces fuel consumption and CO2 emissions by between 5% and 15%, reduces the insurance claims rate by up to 30%, and saves 15% on consumables such as tyres and brakes), raising employee awareness of eco-driving becomes strategic and essential for businesses.
A practical training issue
For industrial vehicles, it is not just about raising employee awareness. Since models are larger and more robust than a light vehicle, they can pose challenges in terms of handling and engine power, which has an immediate impact on the vehicles aerodynamics and, thus, its efficiency. Since they are also intended for off-roading with loads that are often heavy, they are confronted with issues of fuel consumption and safety that are more significant than for other vehicles, as well as greater CO2 emissions due to regular stopping. Thus, proper training is welcome to master eco-driving techniques. While sharing information has an immediate and undeniable impact, implementing a coherent training programme through courses (in-person and/or e-learning), individual coaching, practical exercises, even driving simulators, will help guide employees in the long-term. It also has the advantage of consolidating gains and preventing falling back into old bad habits, while allowing for optimal tracking and improving the company’s overall performance.
Finding the right mix of structure and content
To make sure that employees’ training in eco-driving industrial vehicles reaches its full potential, we need to find the right formula. In the face of environmental and safety challenges, the range of education on offer has expanded, and the number of structures offering courses has skyrocketed. At this stage, we can now count hundreds throughout Europe. Between dedicated training institutions (for instance in France: LFP Formations, l’Institut VEDECOM, Agiroute, Develter (interactive courses and simulators), Vanberg, and in Spain: Fenadismer, IDAE, RACE, RACC) organisations specialised in inspections and delivering certifications, insurers, vehicle manufacturers and driving schools, there is a vast number of choices. Vehicle rental companies also offer courses that combine prevention with simulation. For example, FRAIKIN has developed the FRAIKIN Safety Academy, a customisable offer of training and support that maximises practical experience. From light duty to heavy duty, and depending on the choices of the customers, a training session can last from half a day to a full day. Another crucial point to consider when taking your decision is the training course’s structure and materials. Ideally, it should combine theoretical teaching with practical workshops and, more importantly, vary the materials used to maximise employees’ retention. As for Fraikin, sessions include a practical session after a theoretical session. Finally, do not neglect support measures (providing additional resources and material, flexibility, moving around the companies’ facilities) that also play a role in their learning journey.
Also worth reading
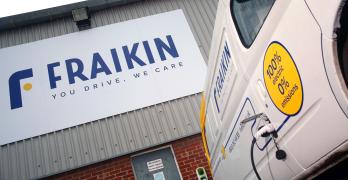
Tackling common EV misconceptions
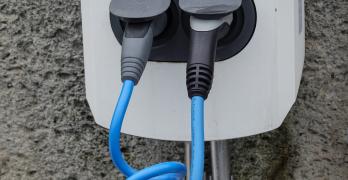
Charging stations: how do you choose the right power?
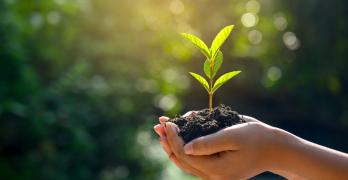