The domino effect of geopolitics on automotive supply chains
- 08/02/24
- 4 min
Many automotive experts projected that the impact of Brexit or the continued development of alternative fuels would be the talking points of the early 2020s. However, no one could have predicted that a global pandemic, rapid inflation and two significant conflicts would grab the headlines.
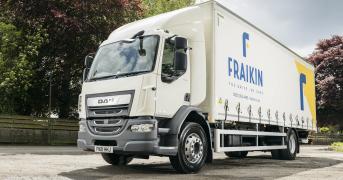
Just as the industry had seemingly stabilised after several challenging years, the escalating tensions in the Middle East have presented a fresh, yet familiar, hurdle for it to face – supply chain uncertainty.
When historians look back on the 2020s, there will certainly be plenty to discuss. While the 20th century’s ‘Roaring 20s’ saw a decade of post-war optimism and relative prosperity before the Great Depression of 1929 struck, its 21st century equivalent seems to have skipped straight to the end of the script. Having already witnessed Covid-19, widespread economic uncertainty, conflict, and numerous natural disasters, all before the decade’s halfway mark, many could be forgiven for keeping their glass half empty.
The latest event to have a global impact is the continued geopolitical instability in the Middle East, which, beyond the immediate and tragic human consequences, is adding another headache for industries across the world.
The crux of the issue sits with the inability of cargo ships – filled with the valuable parts, tools and equipment needed to manufacture cars, vans and trucks across Europe – to safely navigate their usual Middle Eastern shipping lanes. Given approximately 15% of world shipping traffic travels via the Suez Canal – which is also the shortest shipping route between Europe and Asia – this is the last thing an automotive industry still recovering from the pandemic needed.
To protect their crew and cargo, a high volume of ships are instead being diverted through alternative lanes – typically around Africa – which in some cases adds four to six weeks on imports bound for the UK and Europe. This of course impacts the vehicle manufacturing itself, and as a knock-on effect, the planned deliveries to their customers.
With the conflict in Gaza and Israel having now been underway for several months, Europe’s key automotive manufacturing stakeholders are starting to really feel this domino effect. For instance, both Tesla and Volvo Cars announced in January that they were suspending some production in Europe, with the former citing that a lack of components and delivery delays were “creating a gap in supply chains,” with Elon Musk predicting the halt would see a drop in production of between 5,000 and 7,000 cars.
It is not just the passenger car market which has been affected, however. During Fraikin’s regular conversations with the major commercial vehicle manufacturers, we are also seeing delivery and manufacturing delays, with the same issues apparent when sourcing replacement parts for repairs and servicing.
It is a situation which Fraikin is not just acutely aware of, but actively tackling head-on. Our team are proactively monitoring and tracking price fluctuations across our supply base, managing operational and servicing risks – including spiking VOR costs – as well as working tirelessly to ensure our stocked parts capacity remains at expected levels.
Meanwhile, for Fraikin customers awaiting vehicle deliveries, we remain in constant communication with vehicle manufacturers to minimise disruption and cost impacts for all our clients.
While the status of the supply chain today is no doubt frustrating for many stakeholders, the memory of delayed deliveries and closed manufacturing plants during the pandemic – with a global semiconductor chip shortage that is still ongoing – may mean that for many the current outlook feels very familiar.
But how could the industry avoid such delays moving forward?
Just-in-time manufacturing has been the go-to production method for the automotive industry for decades, but can suppliers and vehicle manufacturers continue to rely on this model? New investments – from both the public and private sectors – in facilities such as battery manufacturing plants and EV charging infrastructure suggest a growing appetite for players to centralise key parts of their supply chain and reduce their reliance on external partners.
Such a transformation, however will not happen overnight, but in the meantime, you can rest assured that Fraikin remains committed to deliver a better day for all our customers.
Also worth reading

Transport: The promise of hydrogen
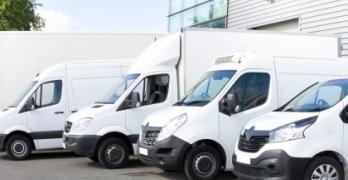
Semi-trailer: cold for performance
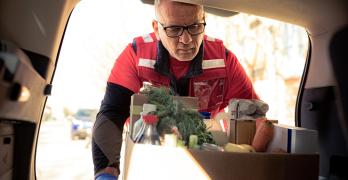