Semi-trailer: cold for performance
- 24/08/23
- 6 min
EPISODE #3: SEMI-TRAILER SERIES – Once upon a time there was… the history of artificial cold! It all began in the middle of the 19th century, when the rural exodus led to the disappearance of the short supply chain and it became necessary to preserve foodstuffs in a new way. Because it is essential to guarantee an optimal cold chain to its customers, let’s discover the innovations in the service of refrigeration performance.
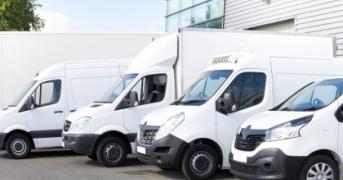
Charles Tellier, a French engineer, developed several techniques for keeping food cold: he created the first refrigerating machine using liquefied ammonia gas and the world’s first meat preservation plant. In 1870, he converted a ship and insulated the hold, and the ship was named “Le Frigorifique”. The Atlantic crossing was a success: after 105 days, the 30 tons of meat arrived in Argentina in very good condition.
It was the American inventor Frederick McKinley Jones, co-founder of Thermo King, who a few years later made many technological advances to improve the long-distance transport of perishable goods.
That was the beginning of the cold chain… Since then, standards and science have only progressed to allow our food, in particular, to be preserved in an optimal manner during its journey to our plates.
Cold: different temperatures for different products
Several “refrigeration systems” are necessary for the proper preservation of consumer products, depending on whether they are fresh (PFT – traditional fresh products), industrial (PFI – industrial fresh products), or frozen. All of this is governed by the ATP regulation (Agreement on the International Carriage of Perishable Foodstuffs), in force in more than 50 countries.
Each product has its own cold management. Fresh products are transported at a temperature of between +2 and +15 degrees, depending on the type of food: this is positive cold. For frozen products, the temperature must be maintained between -18 and -25 degrees: this is negative cold. As all food categories are also sensitive to humidity levels, the hygrometry must also be taken into account during transport.
Biotech: spearheading refrigeration innovation
Health products derived from biotechnology are becoming more widespread; one out of every two medicines placed on the market is heat-sensitive, so products derived from living cells have also had to tighten their regulations, particularly with regard to their transport.
Refrigerated transport: breakdown of a refrigerated semi-trailer
The refrigerated vehicle consists of an insulated box, which is powered by a refrigeration unit.
The bodywork is usually insulated with expanded polystyrene and covered with insulating materials: smooth polyester or metal panels
Did you know? As vacuum is the best insulator, there are more and more innovations in double-walled, vacuum-insulated bodies. “We are only at the beginning of vacuum insulation, the vehicles equipped with this solution are prototypes; however, this solution has a bright future,” says Rémi Paign, Fraikin consultant.
There are several types of crates: double-deck, single-temperature or multi-temperature (partitions divide the crate and allow several temperatures to be managed). Some crates are also dedicated to the transport of meat or flowers and require specific arrangements.
Historically, the refrigeration unit consists of a compressor, an evaporator and a condenser. Traditionally, the refrigeration unit is powered by a diesel engine, but on carriers it can be driven by the vehicle’s engine. As this fuel consumes fossil energy and generates noise, it is necessary to ensure that the technology used is in line with new trends.
Semi-trailers: alternatives for a more environmentally friendly cooling unit
CNG, LNG or biodiesel, electricity, new energies are gradually replacing traditional vehicle engines. One of them, CNG, or compressed natural gas, is becoming more and more widespread. Fraikin has supported Fresh&Loc, the logistics specialist of the Globe Express group, in the supply of a fleet of seven CNG-powered refrigerated vehicles.
A hydrogen-powered chiller: solution of the future
Several bodybuilders and manufacturers are testing hydrogen power, which is converted into electricity using a fuel cell. This is a green (if the hydrogen is of low-carbon origin) and silent technique that provides two days of long-distance autonomy and a supply in ten minutes!
Cryonics: a promising alternative
The refrigeration unit uses liquid nitrogen at -196°C which is passed through a heat exchanger, cooling the load compartment twice as fast as a diesel refrigeration unit, while reducing the carbon footprint by 80%!
Thanks to its partnerships with Chéreau and Air Liquide, Fraikin has been able to deploy cryogenic technology to apply it to semi-trailers. Fraikin’s experts participated in the development of this technology at the request of the U group . Indeed, U Logistics wanted to rent CNG-powered road tractors and semi-trailers equipped with a liquid nitrogen refrigeration unit, in order to initiate a real sustainable development approach.
The air curtain to conserve temperature
In order to keep the body cold when the doors are opened, an innovative air curtain system is installed at the rear of the trailer.
“Before, we used to place plastic slats to prevent temperature loss when the trailer doors were opened,” explains Olivier Dutrech, Fraikin’s innovation director.
Now, “The air curtain takes ambient air from inside the body or outside (depending on the manufacturer) and propels it at high speed and low width towards the floor. We create an air gap,” adds Rémi Paing.
The PIEK label: a guarantee of silence for cold and discreet deliveries
“We are working on reducing the noise footprint of the vehicle as a whole. For a refrigerated semi-trailer, this means a low-noise refrigeration unit, sound-absorbing materials inside the semi, and a tailgate with a specific coating to limit noise as much as possible,” adds Olivier Dutrech.
In addition to ensuring that the environment is respected by emitting as little CO2 as possible, innovative technologies are also used to reduce noise pollution. More and more cities are requiring transporters to deliver at specific times, especially at night, to avoid disturbing local residents and to keep traffic moving during the day.
To meet this constraint, the PIEK certification, recognised in the Certibruit approach, guarantees that vehicles making deliveries between 11pm and 7am do not exceed 60 decibels.
The regulations, whether they come from environmental measures or to ensure our health, push the industry to reinvent itself for a permanent innovation of the cold. Whether it is the body or the motorisation of the refrigeration unit, there are many areas for improvement to ensure an optimal cold chain for all players in the sector, as well as full compliance with legislation
Also worth reading
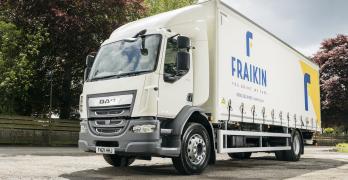
The domino effect of geopolitics on automotive supply chains

Transport: The promise of hydrogen
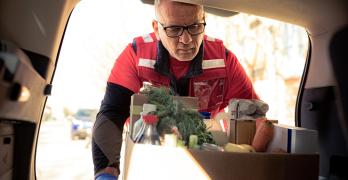