How can the payload of a refrigerated vehicle be optimised?
- 14/04/23
- 4 min
More than ever, optimising the payload of refrigerated vehicles is a central issue in an expanding market. And the health crisis has been a sharp reminder of this, both in terms of volumes and the complexity of constraints, as illustrated by the transport of vaccines.
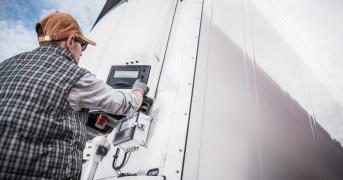
The Payload of a light commercial vehicle (LCV) or lorry is the difference between the Technically Permissible Maximum Mass and its Unladen Weight. There is a simple formula: PL = TPMM – UW
Please note: the unladen weight (UW) value does not necessarily appear on the registration certificate. This value is different from that of the usable volume (expressed in m3), although the two are linked. In addition, we can keep in mind that the heavier a vehicle is when unladen, the lower its payload.
Optimising payload: a growing necessity
With a global refrigerated logistics market that has been growing for several years, the issue of vehicle loading has also become more important in the face of a stricter regulatory context. Because the legislative constraints (*) relating to pollution have become progressively stricter in Europe: control of polluting emissions and vehicle noise, Low Emission Zones (formerly Reduced Traffic Zones), etc. Since vehicles cannot be stacked up for obvious economic reasons, efforts must be made to make their use as efficient as possible. On the other hand, more cyclical developments in food distribution, such as the return of convenience stores in urban areas and the boom in home delivery and services, have increased the need for refrigerated vehicles (lorries, LCVs, etc.) tenfold, making the optimisation of transported volumes an unavoidable challenge.
The global refrigerated logistics market has been growing for several years (from 6.3 billion euros in 2018 to 10 billion euros in 2025 in France alone). There are several issues that now need careful consideration when looking at this market and optimising payloads:
- vehicle loading has become more important in the face of stricter regulations
- the legislative constraints (*) relating to pollution have become progressively tighter in Europe: control of polluting emissions and vehicle noise, Low Emission Zones (formerly Reduced Traffic Zones), etc.
- vehicles cannot be stacked up for obvious economic reasons, efforts must be made to make their use as efficient as possible
- more cyclical developments in food distribution, such as the return of convenience stores in urban areas and the boom in home delivery and services, have increased the need for refrigerated vehicles of all sizes, making the optimisation of transported volumes an unavoidable challenge
What avenues should be explored for refrigerated trucks?
To initiate a payload optimisation process, we can first look at good practice:
- Systematic pursuit of the 100% loading target, which may sometimes involve the adoption of the latest palletising techniques;
- Implementation of processes to “hunt” for “light” or empty trips, which can also involve the adoption of route optimisation software, as the range of products available on the market is increasingly vast and efficient;
- Regular checking of cooling equipment, but also of equipment such as insulation seals;
- Eco-driving, training of user drivers for driving, of course, but also to optimise energy loss linked to door opening and delivery times, etc.
Beyond that, maintaining a high level of payload is a common objective for manufacturers and transporters. The consumption of refrigerated lorries is therefore the subject of in-depth work using alternative energies. Their design and conversion are also drivers of innovation, the rise of self-supporting structures being a perfect illustration: adaptable to different chassis, the floor, often made of aluminium, can preserve or even maximise the payload. These solutions have already been tried and tested on 3.5-tonne combustion engine vehicles, which now have one tonne of payload. This has been possible for several years now. They can also, of course, be used with alternative energy vehicles.
Innovations also concern the refrigeration unit itself
In addition, the refrigeration unit is also the subject of numerous initiatives, which were highlighted at the last Solutrans international trade fair. In order to produce cold more frugally and thus optimise volume and loading capacity, we are seeing the emergence of more compact units and new technologies, such as hydroelectric or cryogenic nitrogen. Boost charge options or HEE (High Energy Efficiency) products are also relevant, depending on the size and use of the vehicles, naturally.
Finally, the vehicle’s fittings also have a role to play: better sizing of compartments via fixed and/or liftable partitions, shelving systems, etc. We must not forget the fundamentals of safety, such as lashing rails, which are useful not only for securing but also for better distributing the goods transported, and “specific business” applications (e.g. meat hanging solutions and hooks).
All of these elements increase the efficiency of refrigerated vehicles, regardless of their size.
(*)
Also worth reading
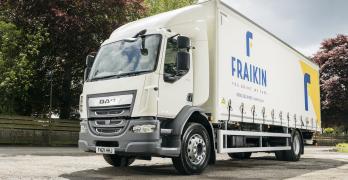
The domino effect of geopolitics on automotive supply chains

Transport: The promise of hydrogen
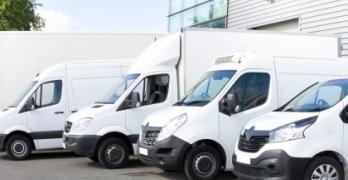